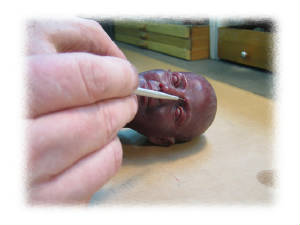
|
The
casting process begins with the creation of an original sculpture The SNOWY OWL shown here is created in French Modeling
Wax. Other materials used may be clay, epoxy, wood or plastic.
|
Molding is next and using liquid rubber. A mold container is constructed around the sculpture
allowing a mass to serve as a heat sink for direct metal casting. This delicate step may take as little as one day or as many
as four weeks depending on the complexity and size of the original sculpture.
|
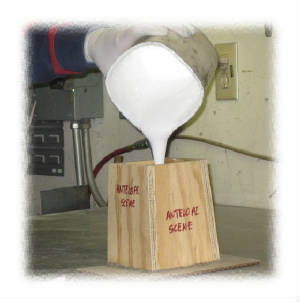
Pouring
Liquid Rubber
|
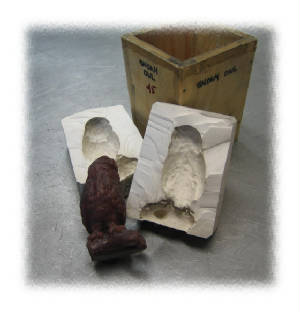
The original mold, many hours later...
|
After the mold rubber has cured, the frame is removed, and the mold is cut apart reveiling the
original model. The wax or clay model is removed and the cavity left is prepared for molten metal, poured directly into the
original mold.
|
Fine Pewter is an alloy of Tin with antimony and copper and has a melting point of 425
degrees F.
Bronze is an alloy of Copper with tin and has a melting point of 950 degrees F.
No lead
is used in the Cordsen Design Studios products.
The temperature at pouring is somewhat higher than the melting
point allowing the metal to flow into all details of the mold.
|
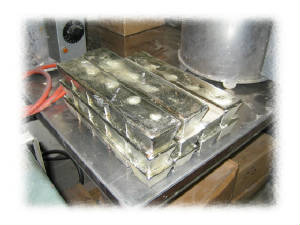
Metal
bars to melt in the all electric furnaces see below...
|
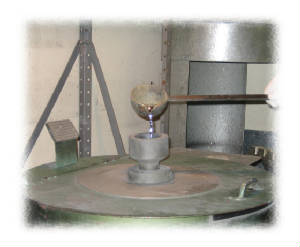
The mold may be spin cast if the mass is not too great. This forces the molten
metal into fine detail and is used for small figurines, animals and ornaments with thin sections.
|
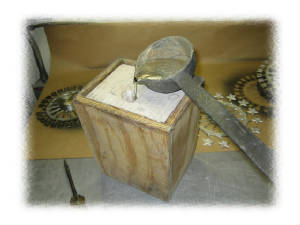
Gravity or vacuum casting is used on larger sculptures when there is a heavy mass. Care must be
taken to allow the metal smooth flow into the cavity without overheating, causing a faulty cast or distortion.
|
After a cooling, the casting is removed from the mold, sprues and vents trimmed and correction
of any flaws from casting begins.
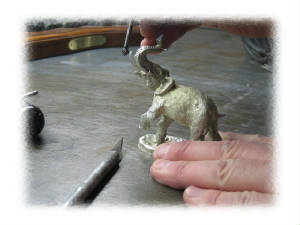
|
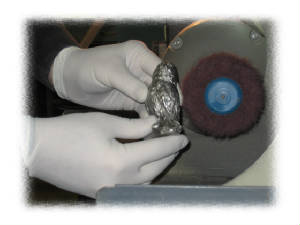
The patina is the final process. Depending on the desired look, this is achieved by use of acids,
enamels, urethanes or metal dyes. The finished sculpture is sealed with clear lacquer and waxed to retain its lustre.
|